Precision in Production: Weighing the Differences Between Weight and Volume Batching
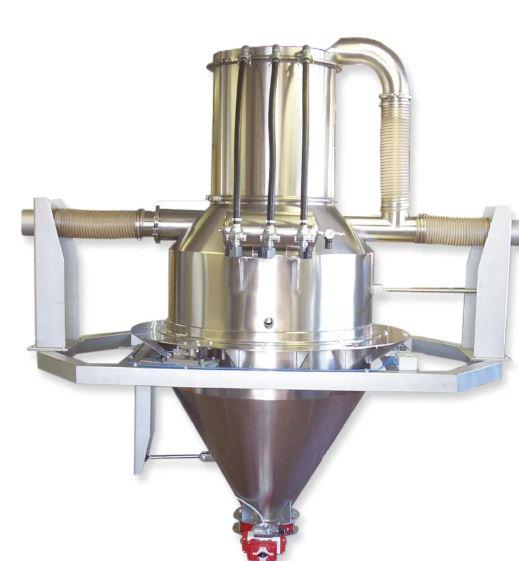
In the world of industrial production and manufacturing, precision and consistency are paramount. Two primary methods have emerged as stalwarts in the quest for accurate material measurement: weigh batching and volume batching. These techniques, while serving similar purposes, operate on fundamentally different principles and offer distinct advantages and challenges in various applications.
Understanding Weight Batching
Weight batching, also known as gravimetric batching, is a method that relies on the measurement of mass to determine the quantity of materials in a batch. This process typically employs sophisticated batching scales and load cells to ensure precise measurements.
Key features of weight batching include:
- High accuracy, often within 0.1% of the target weight
- Consistency across different material densities
- Ability to handle varying moisture content
- Suitability for a wide range of materials, from fine powders to large aggregates
Exploring Volume Batching
Volume batching, or volumetric batching, measures materials based on their volume rather than their weight. This method often uses pre-calibrated containers, flow meters, or displacement techniques to measure the quantity of materials.
Characteristics of volume batching include:
- Simplicity in setup and operation
- Lower initial equipment costs
- Faster processing times for certain materials
- Effectiveness for liquids and gases
Comparative Analysis: Weight vs. Volume Batching
Aspect | Weight Batching | Volume Batching |
---|---|---|
Accuracy | High (±0.1% to 0.5%) | Moderate (±1% to 5%) |
Consistency | Excellent across materials | Varies with material properties |
Initial Cost | Higher | Lower |
Maintenance | Regular calibration required | Less frequent maintenance |
Speed | Can be slower for some materials | Generally faster |
Material Suitability | Wide range, including varying densities | Best for consistent materials |
Applications and Industry Preferences
The choice between weight and volume batching often depends on the specific industry and application. Here's a breakdown of common preferences:
Weight Batching Dominance
- Pharmaceutical Industry: Requires high precision for active ingredients
- Food Production: Ensures consistent recipes and nutritional content
- Chemical Manufacturing: Maintains precise ratios for reactions
- Construction: Accurate concrete mixing for structural integrity
Volume Batching Preference
- Beverage Industry: Efficient for large-scale liquid bottling
- Oil and Gas: Measurement of fluid flows
- Agriculture: Distribution of liquid fertilizers
- Paint Manufacturing: Mixing of liquid components
Technological Advancements in Batching
The field of batching has seen significant technological advancements in recent years, particularly in the realm of weight batching. Modern weighbridge manufacturers are at the forefront of these innovations, producing sophisticated systems that offer:
- Integration with IoT (Internet of Things) for real-time monitoring and data analysis
- AI-driven predictive maintenance to minimize downtime
- Advanced software for recipe management and production optimization
- High-precision load cells capable of accuracies up to ±0.01%
- Automated calibration processes for maintaining accuracy over time
Note: While volume batching technologies have also improved, the inherent limitations of volumetric measurement have kept weight batching at the forefront of high-precision applications.
Environmental and Economic Considerations
The choice between weight and volume batching can have significant environmental and economic implications:
Environmental Impact
Weight batching often leads to:
- Reduced waste due to higher accuracy
- Lower energy consumption in the long run due to fewer errors and reworks
- More efficient use of raw materials
Volume batching may result in:
- Potentially higher material waste due to lower accuracy
- Lower initial environmental impact from simpler equipment manufacturing
Economic Factors
Weight batching considerations:
- Higher initial investment in equipment
- Lower long-term costs due to reduced errors and waste
- Potential for higher product quality and customer satisfaction
Volume batching considerations:
- Lower upfront costs
- Potentially higher ongoing costs due to material waste and quality control issues
- Faster production speeds in some applications, leading to higher throughput
Challenges and Solutions in Batching
Both weight and volume batching face unique challenges in industrial applications. Understanding these challenges and their solutions is crucial for optimizing production processes.
Challenges in Weight Batching
- Vibration Interference: Can affect accuracy of weight measurements
- Temperature Fluctuations: May impact load cell performance
- Material Flow Issues: Sticky or bridging materials can cause inconsistent feeding
Solutions include:
- Advanced vibration dampening systems
- Temperature-compensated load cells
- Specialized feeding mechanisms for difficult materials
Challenges in Volume Batching
- Material Density Variations: Can lead to inconsistent batch quantities
- Aeration of Powders: Affects apparent volume
- Moisture Content Changes: Impacts volume measurements
Solutions include:
- Regular recalibration based on material density
- De-aeration systems for powders
- Moisture sensors for real-time adjustments
Future Trends in Batching Technology
The future of batching technology is likely to see further integration of smart technologies and a move towards more sustainable practices:
- Artificial Intelligence: For predictive maintenance and self-optimizing systems
- Blockchain Integration: To ensure traceability and transparency in supply chains
- Sustainable Materials: Development of eco-friendly sensors and equipment
- Hybrid Systems: Combining weight and volume measurements for optimal accuracy and speed
- Miniaturization: Smaller, more efficient batching systems for specialized applications
Conclusion: Making the Right Choice
The decision between weight batching and volume batching is not always straightforward. It requires careful consideration of various factors including:
- Required accuracy and consistency
- Nature of materials being handled
- Production volume and speed requirements
- Initial budget and long-term cost considerations
- Industry standards and regulatory requirements
While weigh batching generally offers superior accuracy and consistency, volume batching can be the more practical choice in certain applications. As technology continues to advance, the gap between these methods may narrow, potentially leading to more hybrid solutions that leverage the strengths of both approaches.
Ultimately, the key to successful batching lies in understanding the specific needs of your production process and choosing a method that aligns with your quality, efficiency, and economic goals. Consulting with experienced weighbridge manufacturers and batching experts can provide valuable insights to guide this critical decision.
Remember: In the world of industrial production, the right batching method can be the difference between mediocrity and excellence, waste and efficiency, profit and loss. Choose wisely, and let precision be your guide to success.